failure of cutting tool
Whenever the tool is not performing the machining operation satisfactorily, then there is a failure of cutting tool.
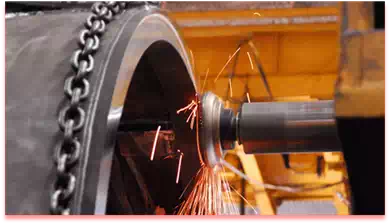
The following draw backs are observed if the tool failure occurs.
1. The tool ceases to produce the work-piece according to the required dimensions.
2. The tool gets overheated.
3. Excessive surface roughness is observed.
4. Forces and power consumption increases.
5. Sometimes the burnishing brand will appear on the work piece.
6. Produces vibrations during machining.
The parameters used for measurement of satisfactoriness of machining is
1. Surface finish produced on work piece
§ At the beginning of machining operation it is found that excellence and mirror like finish is produced on work piece.
§ After sometimes when the lines are produced on machined surface, it is assumed that surface finish is reduced and tool is failed.
2. Forces induce during machining:
§ By connecting dynamo meter to the work table, the forces in machining will be measured online.
§ Whenever the increase in forces is taking place it is assumed that tool has been failed.
§ By connecting Ammeter to the input of electrical motor, the current drawn by motor will be measured online.
§ Whenever the increase in current drawn by motor is greater it is assumed that tool has been failed.
§ The temperature of chip can measured by observing the color of chip formed.
§ During normal satisfactory machining conditions the color of chip is light Blue or metallic color.
§ When the machining is done with failure tool, because of higher heat generation the color of chip is turned to black or burnt color.
§ From the above whenever the color of chip is observed to be black or burnt color, tool is assumed to be failed.
§ During machining of high carbon work pieces, whenever white colored gases are observed, it is assumed that tool is failed.
Modes of tools failure:
1. Failure through plastic deformation
2. Failure through mechanical breakage
3. Failure through mechanical gradual wear
1. Plastic Deformation Failure:
Whenever the tip of tool is experiencing temperature greater than hot hardness temperature of tool material, it is losing its hardness considerably and the tip of tool is deforming plastically called as plastic deformation failure of the tool.
Reasons for plastic deformation failure:
1. Wrong selection of tool material.
2. Wrong selection of process parameters.
2. Mechanical Breakage Failure:
A cutting tool gets broken due to the following factors:
1. Large cutting force.
2. By developing fatigue cracks under chatter conditions.
3. Weak tool materials.
4. High temperature and high stress.
In this also failure duration is repeatable.
Therefore it is also considered as abnormal failure of tool.
3. Mechanical Gradual wear failure:
During machining operation, the tool is wearing out and slowly and whenever the wear become considerable, it can’t perform the machining satisfactory called as gradual wear failure.
The gradual wear takes place due to
1. Crater wear and
2. Flank wear
Crater wear:
§ The major tendency for wear is due to the abrasion between the chip and the face of the tool, a short distance from the cutting edge.
§ The crater (a shallow spherical depression present on surface) is formed on the surface of the tool by the nation of chip particles flowing over it because of very high temperature.
§ When Cratering becomes excessive, the cutting edge may break from the tool.
§ Cratering is commonly observed while machining ductile materials, which produce continuous chips.
Reasons for crater wear:
§ Presence of friction between chip – tool interference.
§ Abrasive action of microchips present at chip – tool interference.
§ Abrasive action of fragments of built up edge present at chip-tool interface diffusion wear.
Flank wear:
Wear taking place on flank face of tool is called as flank wear.
Reasons for flank wear:
1. Presence of friction at tool interface.
2. Abrasion action of microchips present at tool work interface.
3. Diffusion wear.
No comments:
Post a Comment