RAPID PROTOTYPING
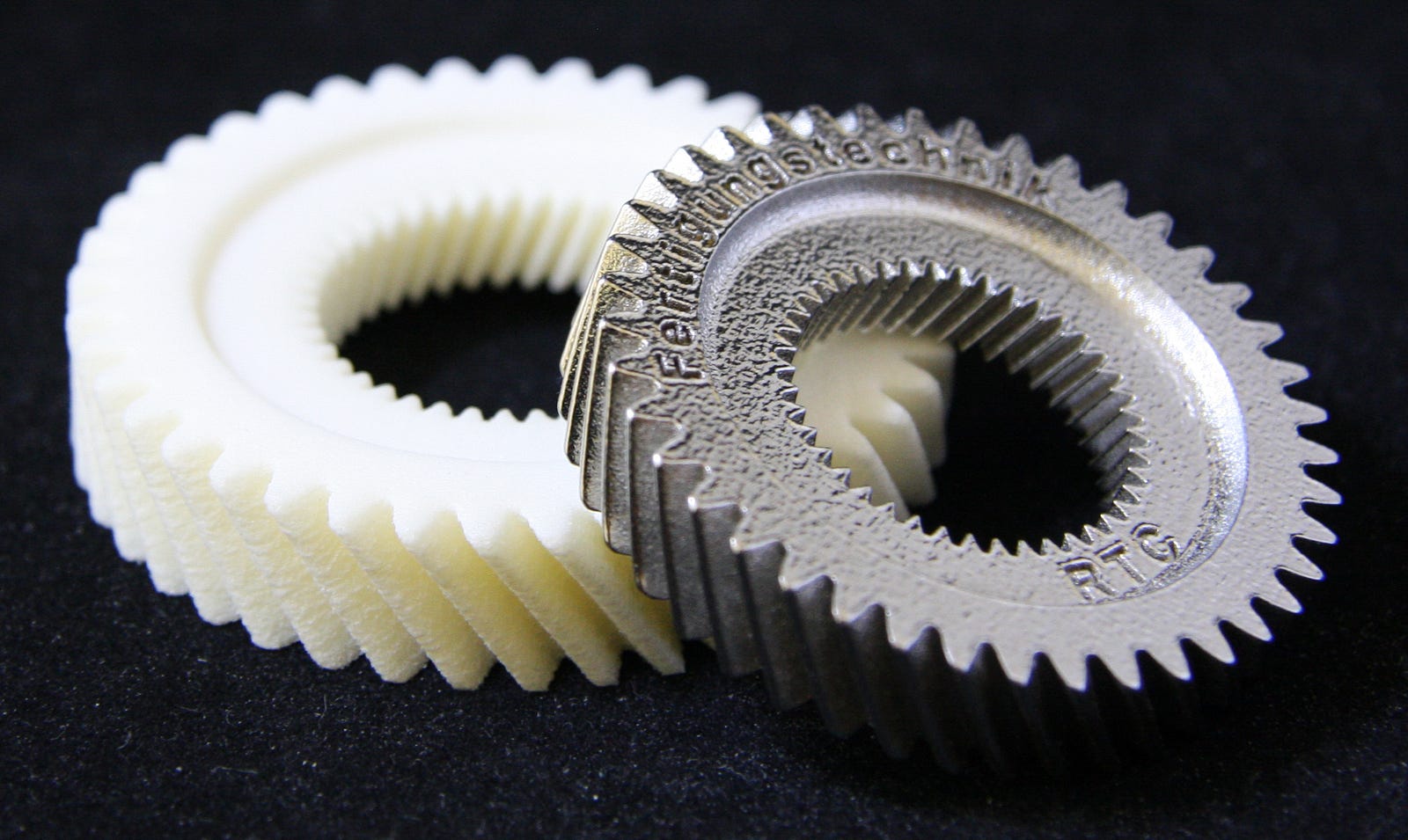
This paper deals
with” RAPID PROTOTYPING” as in
conventional machining process. Rapid prototyping refer to creation of
three-dimensional objects directly from CAD files. And it is the automatic
construction of physical objects using solid freeform fabrication. System of
rapid prototyping to a set of processes in which the physical object is
obtained directly from its cad model without explicitly going through the
various steps of manufacturing which includes tooling and material removal.
Rapid prototyping system using base materials are thermoplastics, metal
powders, eutectic metals, photopolymer, titanium alloys and various materials.
It advantages is offers direct manufacturing from cad files and sketches and
paperless manufacturing, very past development of functional parts is possible,
it offers greater capability to compute mass properties of components and
assemblies.
INDRODUCTION
Rapid prototyping starts with
quick creation of manufacturing ready, CAD models; continues to verify the
design using CAE (computer aided engineering) tools.the first techniques for
rapid prototyping became available in the late 1980s and were used to produce
models and prototypes parts. Today, they are used for a much wider range of
applications and are even used to manufacture production quality parts in
relatively small numbers. Some sculptors use
the technology to produce complex shapes for fine arts
exihibition.In rapid prototyping,the machine reads in data from a CAD drawing
and lays down successive layers of liquid, powder, or sheet material, and in
this way builds up the model from a series of cross sections.
PROTOTYPING
Prototyping can
resolve uncertainty about how well a design fits the user's needs. It helps
designers to make decisions by obtaining information from users about the
necessary functionality of the system, user help needs, a suitable sequence of
operations, and the look of the interface.
PROTOTYPING METHODS
Various kinds of
prototyping have been developed to obtain different kinds of information such
as requirements animation, rapid, incremental, and evolutionary prototyping.
v Requirements
animation,
in most cases used to demonstrate functionally, is construed in the software
prototype that can be assessed by users.
v Rapid prototyping is a form of collecting
information on requirements and on the adequacy of possible designs.
v Incremental
prototyping
enables large systems to be installed in phases to avoid delays between
specification and delivery.
v Prototyping
evolutionary
considered to be the most involved form of prototyping, is a compromise between
production and prototyping.
RA