FUEL FROM WASTE PLASTICS
Plastic have become an integral part of our lives. Relatively low cost and being easily available have brought a use and throw culture. Each year more than 100 million tones of plastics are produced worldwide because of use and throw culture so plastics waste management has become a problem worldwide. This paper, explain the process of converting waste plastic into value added fuel through recycling. Thus two universal problems such as Problems of waste plastic and Problems of fuel shortage are being tackled simultaneously. The waste plastics are subjected to depolymerisation, fractional distillations to obtain different value added fuels such as petrol, kerosene, and diesel, lube oil, furnace oil traction and coke. The process of waste plastic into fuels can literally change the economic scenario of our country. Thus, process of converting plastics to fuel has now turned the problems into an opportunity to make wealth from waste.
Key Words: Waste plastics, Reactors, Depolymerisation and Fractional distillation.
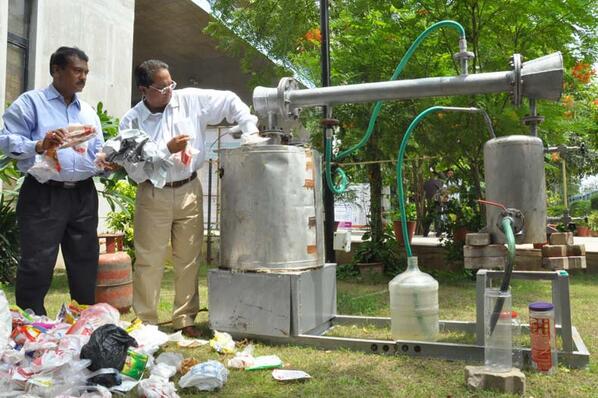
Introduction
Degradability of different waste materials:
Degradability of different waste materials:
SL. NO.
|
TYPE OF PRODUCTS
|
TIME TAKEN TO
DEGENERATE
|
1
|
Organic waste, etc.
|
1 to 3 weeks
|
2
|
Paper
|
1 to 3 weeks
|
3
|
Cotton cloth
|
8 to 20 weeks
|
4
|
Wood
|
10 to 15 years
|
5
|
Wooden items.
|
10 years
|
6
|
Tin, Aluminium&Metals
|
100 to 500 years
|
7
|
Plastics
|
Million years
|

Yield
NAME OF THE PRODUCT
|
AMOUNT IN PERCENTAGE
|
Liquid Distillate
|
110 % - 115 %
|
Coke
|
05% - 10%
|
Gas
|
18 % - 22%
|
LPG
|
14% - 16%
|
Hydrogen etc
|
01% - 02 %
|
FUELS
|
PERCENTAGE
|
Gasoline
|
60%
|
Diesel
|
30%
|
Lubricating Oil
|
8 –10 %
|
SL.NO.
|
SPECIFICATIONS
|
Regular
PETROL
|
PETROL FROM WASTE PLASTIC
|
1.
|
Specific Gravity at 280 C
|
0.7423
|
0.7254
|
2.
|
Specific Gravity at 150 C
|
0.7528
|
0.7365
|
3.
|
Gross Calorific Value
|
11210
|
11262
|
4.
|
Net Calorific Value
|
10460
|
10498
|
5.
|
Aniline Point In 0 C
|
48
|
28
|
6.
|
Aniline Point In 0 F
|
118.4
|
82.4
|
7.
|
Flash Point
|
23
|
22
|
8.
|
Pour Point
|
< -20 0 C
|
< -20 0 C
|
9.
|
Cloud Point
|
< -20 0 C
|
< -20 0 C
|
10
|
Reactivity With Ss
|
NIL
|
NIL
|
11.
|
Reactivity With Ms
|
NIL
|
NIL
|
12.
|
Reactivity With Cl
|
NIL
|
NIL
|
13.
|
Reactivity With Al
|
NIL
|
NIL
|
14.
|
Reactivity With Cu
|
NIL
|
NIL
|
15.
|
Octane Rating
|
83
|
95
|
16.
|
Mileage
|
44.4
|
44.0
|
17.
|
Time for 0-60 KMPH
|
22.5 S
|
18.1 S
|
18.
|
Co % At 400 RMP/Hc
|
2.8
|
3.5
|
19.
|
Comments On Engine Noise
|
MORE
|
LESS
|
Process brief for 1 KG input and the yield of output:
INPUT
|
QTY
|
RATE
PER KG
|
AMOUNT
(RS).
|
OUTPUT
|
QTY
( LITER)
|
RATE
PER
LITER
|
AMOUNT
(RS).
|
PLASTIC
|
1.00
|
2.00
|
2.00
|
PETROL
|
0.600
|
37.50
|
22.50
|
LABOUR
|
5.00
|
DIESEL
|
0.300
|
25.50
|
7.65
| ||
SERVICE
CHARGE
|
2.50
|
LUBE OIL
|
0.100
|
15.00
|
1.50
| ||
TOTAL
|
1.00
|
9.50
|
1.00
|
31.65
|
· Shreeve’s Handbook of Chemical Engineering.
· Jatropha Bio-diesel production in University of Bangalore, the Statesman (Teri).
· Ganesnan V ‘IC Engines’, TATA McGraw Hill Book Company- New Delhi.
· Rajput R.K. ‘Thermal Engineering’, Lakshmi Production (P) Ltd.
Plastics play a major role in day-today life, as in certain application they have an edge over conventional materials. Indeed, their light weight, durability, energy efficiency, coupled with a faster rate of production and more design flexibility, have allowed breakthroughs in fields ranging from non-conventional energy, to horticulture and irrigation, water-purification systems and even space flight.
How ever one has to accept that virtues and vices co-exist. Plastics are relatively cheaper and being easily available has brought about use and throws culture. Plastics waste management has become a problem world over because of their non-degradable property. A majority of landfills, allotted for plastic waste disposal, are approaching their full capacity. Thus recycling is becoming necessary.
Plastics in Environment
Three million tones of waste plastics are produced every year in the U.K.alone, only 7% of which is recycled. In the current recycling process usually the plastics end up at city landfills or incinerator. As with any technological trend, the engineering profession plays an important role in the disposal of plastic waste. Discarded plastic products and packaging materials make up a growing portion of municipal solid waste.
The Global Environment Protection Agency [GEPA] estimates that by the year 2004 the amounts of plastic throw away will be 65% greater than that in the 1990’s. The recycling of the plastic is only about one percent of waste plastic in the stream of waste in developing countries as compared to a rate of recycling of aluminum which is about 40% and 20% for paper, where as recycling rate in India is very high up to 20% of waste plastic.
In a short span of five years plastics have captured 40% of total 6.79 billion USD packaging market in India. This situation may grow further in the coming years with more and more US and European companies entering the market. It would be very interesting to note the type of litter we generate and the approximate time it takes to degenerate.
India has been used as a dumping ground for plastic waste, mostly from industrialized countries like Canada, Denmark, Germany, UK, Netherlands, Japan, France and the United States.
Each year more than 100 million tones of plastic are produced worldwide. Though plastics have opened the way for a plethora of new inventions and devices it has also ended up clogging the drains and becoming a health hazard. The plastic waste accounts to about 5600 tons per day in India. At these alarming levels of waste generation, India needs to set up facilities for recycling and disposing the waste.
Technological Process
Several processes and means have been attempted to fight against the alarming levels of waste generation. However each process has its drawbacks and operational, economical and financial limitations for practical implementation. We have to set up a process to overcome the above-mentioned drawbacks and limitations.
Description in process
Generally any waste plastic treatment involves sorting operation, which is a time and energy consuming process. In this process waste plastic can be utilized without any sorting (or) cleaning operation.
The process consists of following operations
1. Loading of waste into the reactors.
2. Depolymerisation of the waste plastic.
3. Collecting the liquid distillate
4. Collecting the combustible gases.
Fractional Distillation
1. Loading of distillate into the distillation furnace,
2. Collecting the fraction of liquid distillate from the distillation tower.
The waste plastic from the landfills are segregated and stored in the storage tank. Using hot air to the reactor where depolymerisation takes place conveys it. The depolymerisation of waste plastic under control batch reactor results in conversion of waste plastic in a mixture of fuels at atmospheric pressure and ambient room temperature.
Liquid fuels consist of Fraction of Gasoline, Diesel, and Lubricating oil. In the process of conversion, by-products such as gases and cokes are also formed. Gases are tested and majority of them are proved to be in the range of LPG. Coke is available as residue in the process, which is again in the form of fuel.
Properties and their Purification of fuels
The properties of liquid distillate match with properties (Ex: specific gravity and pour points) of high quality imported crude. The fuels obtained in the waste plastic process are virtually free from contaminants such as Lead, Sulphur and Nitrogen. In the process (i.e.) the conversion of waste Plastic into Fuels, the properties mentioned above of Petrol & Diesel fractions obtained are of superior quality with respect to regular commercial Petrol and Diesel purchased locally and has been proved by the performance test.
During the process, hazards related to health and safety is reduced to 90% as compared to regular refinery process.
Quality of fuels
The quality of Gasoline and Diesel fractions obtained in the process is not only at par with regular fuels in tests like Specific gravity is 0.7365 /150C CCR (Conradson Carbon Residue) Ash, calorific value etc but it is also better in terms of quality in test like flash point, API gravity.
Additives
Regular fuels obtained from Crude oil like Gasoline and Diesel are subjected to many reactions and various additives are added to improve combustion and meet BIS characteristics before it is introduced to market. However the fuel (Gasoline, Diesel) fractions obtained in the process can be utilized without much processing.
The average percentage output yield of the products in the first phase of reaction depending on the composition of the waste plastic is as follows,
The percentage of liquid distillate is mentioned in terms of weight by volume whereas percentage of Coke & Gas is mentioned in terms of weight by weight. During the second phase of reaction (i.e.) fractional distillation, the average percentage yields of various fuel fractions depending on the composition of the waste plastic are follows,
Comparison of Petrol from waste Plastics with regular Petrol
Feasibility
The production of the fuels from the waste plastic of various sorts has been carried out a number of times to arrive at the unit cost of production. The break - up of the cost for per kg input of the plastic and the related output for the same is depicted in the table below.
Conclusion
Since, the plastics are non-biodegradable, the development in biodegradable plastics are still lagging behind. So it is essential to convert the plastics for some useful purposes in order to reduce the waste plastics to environment. . Thus, the process of converting plastics to fuel has now turned the problems into an opportunity to make wealth from waste. This paper is of greater importance in the present Indian scene in view of the serious energy crisis and is in the interest of national economy.